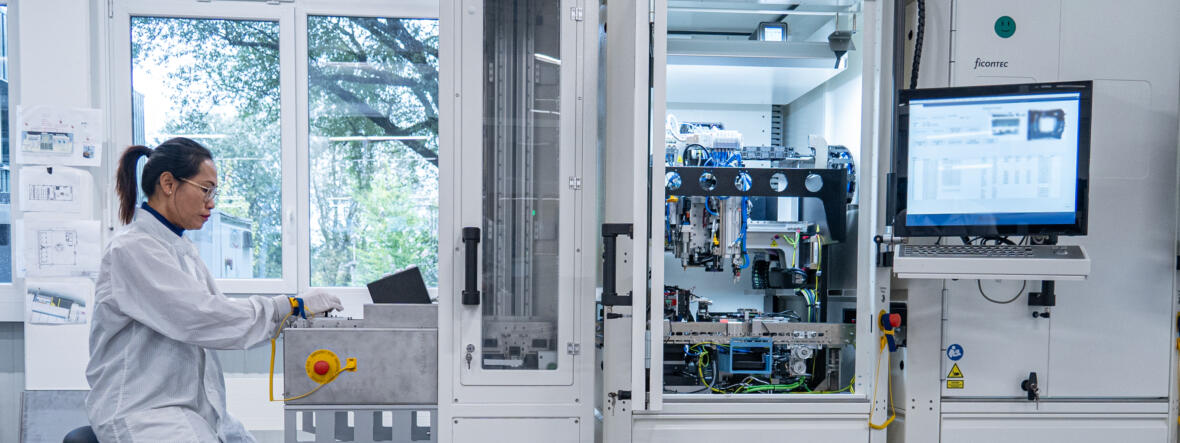
Wie sich Wetzikon und Uster einen Weltmarkt teilen
Die Textilindustrie hat ihre Spuren im Zürcher Oberland hinterlassen. Die Spinnereien sind verschwunden, die Webereien bis auf eine. Doch noch immer ist die Region in einem Bereich Weltklasse.
Nicht einmal zehn Kilometer liegen zwischen der Sonnenbergstrasse 10 in Uster und der Kastellstrasse 10 in Wetzikon. Hier lebt die Tradition der Baumwollindustrie im Zürcher Oberland in Form zweier Unternehmen von Weltklasseformat weiter: Uster Technologies und Loepfe Brothers.
Doch beginnen wir von vorn: Vor rund 200 Jahren kam die industrielle Revolution in Form von Spinnereien und Webereien in der Region an. Der Aabach mit seiner (dank dem Pfäffikersee als Regulierbecken) konstanten Wassermenge und seinem leichten Gefälle war in der damaligen Zeit wie geschaffen für die Nutzung der Wasserkraft.
War in der Region zuvor in Heimarbeit gesponnen und gewoben worden, so setzte in der ersten Hälfte des 19. Jahrhunderts eine eigentliche Gründungswelle von mechanischen Baumwollspinnereien ein. Der Aabach wurde zum «Millionenbach» – nicht für die Textilarbeiter, aber für die Fabrikbesitzer, natürlich.
Rund 100 Jahre war das Zürcher Oberland ein Zentrum der Textilindustrie. Bis sich diese in der zweiten Hälfte des letzten Jahrhunderts nach Fernost verabschiedete. Heute existiert nur noch eine industrielle Baumwollweberei in der Region: die Weberei Russikon, die aus Baumwolle schwere Damaststoffe herstellt.
Die Industrie prägt die Region und umgekehrt
Unzählige Zeitzeugen entlang dem Aabach belegen die einstige Grösse und Bedeutung dieser Industrie – alte, un-oder umgenutzte Fabrikareale, Kleinkraftwerke oder auch die Villen der Fabrikanten. Die Textilindustrie prägte das Zürcher Oberland. Und das Zürcher Oberland prägt die Textilindustrie – bis heute. Zwei Firmen in Uster und Wetzikon besetzen eine Nische, in der sie besser sind als alle anderen: Uster Technologies und Loepfe Brothers haben sich auf die Qualitätssicherung in der Textilindustrie spezialisiert.
Beide sind Tochtergesellschaften von internationalen Konzernen, operieren aber mit grosser Selbständigkeit: Uster Technologies entstand 2003 durch ein Management-Buy-out aus der Zellweger-Luwa-Gruppe und gehört seit 2012 zum japanischen Konzern Toyota Industries Corporation. Loepfe Brothers ist seit 2021 Teil des belgischen Textilmaschinenherstellers Vandewiele.
In Uster begann das Textilgeschäft in den 1930er Jahren. Der Durchbruch gelang 1948 mit dem sogenannten Garn-Gleichmässigkeits-Prüfgerät (GGP) für gesponnenes Garn. 1957 folgte die Uster-Statistik, die die Qualität von Baumwollfasern und Garnen erfasst. Diese Statistik deckte in der Folge immer weitere Qualitätskriterien ab und etablierte sich zum weltweit anerkannten Qualitätsstandard für die Textilindustrie. Bis heute wird die Qualität von Fasern und Garnen in Uster bestimmt.
Eine Stadt benannt nach einer Firma …
Der Standard trägt den Namen Uster in die Welt hinaus. Mit teilweise amüsanten Folgen, wie Davide Maccabruni mit einem Lachen erzählt: «Es kommt vor, dass wir internationale Gäste bei uns empfangen, die begeistert sind, dass die Stadt nach unserer Firma benannt wurde.» Der gebürtige Italiener, der am Politecnico in Mailand Management und Produktionstechnik.
Wenn es um die Qualität von Garnen geht, blicken Spulmaschinenhersteller aus der ganzen Welt ins Oberland.
Zehn Kilometer weiter in Kempten navigiert die Loepfe Brothers Ltd. im selben Geschäftsfeld. CEO Markus Kleindorp leitet das Unternehmen seit Mai dieses Jahrs. Zuvor war der Deutsche mehr als 20 Jahre bei einer Vandewiele-Tochter in Dornstetten (Baden-Württemberg) tätig.
Gegründet wurde die Firma 1955 von den Brüdern Helmut und Erich Loepfe. Zuerst war der Geschäftssitz an der Zypressenstrasse in Zürich, zehn Jahre später folgte der Umzug nach Wetzikon. Begonnen hatte alles mit dem sogenannten Schussfadenführer.
Die optisch-elektronischen Geräte sorgten für die Überwachung des Garns, das sich noch im Eintragssystem der Webmaschine befand. Bei zu kleinem Vorrat wurde der Spulenwechsel automatisch eingeleitet. 1962 folgte der erste opto-elektronische Garnreiniger. Hier überschneiden sich die Produktportfolios der beiden Oberländer Unternehmen.
Mit dem Sensor durch dick und dünn
Loepfe Brothers wie Uster Technologies stellen Bauteile her, die direkt in die Garnspulmaschinen integriert sind. Sensoren überprüfen das Garn nach Dick-und Dünnstellen, aber auch nach kleinsten Verschmutzungen.
«Qualitätssicherung ist daher ein etwas missverständlicher Begriff», sagt Loepfe-CEO Markus Kleindorp. «Wir sind sehr früh eingebunden in den Produktionsprozess.»
In einem Showroom auf dem Firmengelände in Kempten stehen verschiedene Garnspulmaschinen, in denen Sensorik von Loepfe verbaut ist. Es sind kleine, kaum faustgrosse Geräte, bestehend aus Tastkopf und Rechnereinheit. Bis zu 1800 Meter Garn werden pro Minute auf die Spule gewickelt. Der Sensor erkennt auch bei diesen hohen Geschwindigkeiten kleinste Abweichungen im Garn im Millimeterbereich.
Das Engineering erfolgt in Wetzikon. Auch zentrale Teile, beispielsweise optische Komponenten, werden an der Kastellstrasse hergestellt. Weniger bedeutende Bauteile wie Gehäuse werden an Zulieferer vergeben. Die Endmontage wiederum findet in Wetzikon statt.
Uster Technologies entwickelt und produziert auch in den USA und China. Doch der Garnreiniger, eines der wichtigsten Produkte, wird in der Heimatstadt gefertigt.
Der Produktionsstandort Schweiz ist beiden Unternehmen wichtig, die hohen Lohnkosten sind zu verschmerzen. Rund 15 bis 20 Prozent des Gesamtpreises einer Spulmaschine machen die Kosten des Garnreinigers aus. «Der Kunde wählt die Ausstattung und bestimmt so den Preis», erklärt Stefan Imfeld, Head of Materials & Production bei Loepfe. «Entscheidend ist dabei die Anzahl und Art der eingebauten Sensoren.»
Trotzdem habe der Standort Wetzikon heute nur noch «historische Gründe», ergänzt Markus Kleindorp. Denn mit der Textilindustrie sind auch die Kunden für die Garnreiniger aus Uster und Wetzikon weitergezogen. Sie lassen sich an einer Hand abzählen: Heute stammen die Hersteller von Textilmaschinen – abgesehen von Rieter in Winterthur – aus China, Japan und Italien.
Das Risiko, in einen Preiswettbewerb mit Billiganbietern zu geraten, ist in diesem speziellen Segment gering. Fehler im Endprodukt schaden der Reputation des Textilherstellers, und Klagen von Kunden können teuer werden.
Von der einzelnen Baumwollfaser bis zum fertigen T-Shirt im Laden liegen rund 60 verschiedene Prozesse. «Die Fertigung ist sehr kleinteilig, das ergibt Nischen, wie wir eine besetzen», sagt Kleindorp. Bis jetzt sei noch kein chinesischer Hersteller auf die Idee gekommen, die Garnreiniger von Loepfe Brothers oder Uster Technologies zu kopieren oder etwas Eigenes zu entwickeln: «Die Nische ist einfach zu klein.»
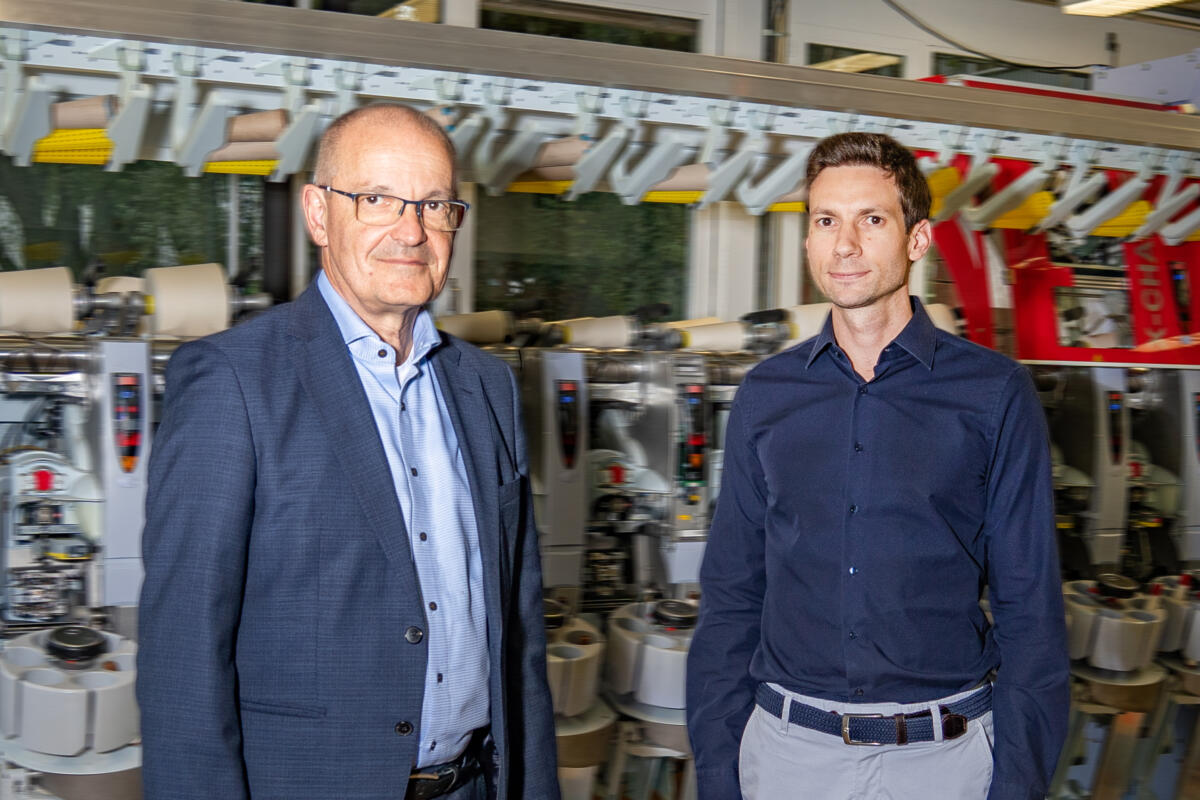
Das Textilgeschäft ist zyklisch
Bei den Garnreinigern überschneiden sich die Produktportfolios der beiden Oberländer Unternehmen. Uster Technologies stellt neben Systemen, die die Qualität während eines Prozesses überwachen, auch Labortestgeräte zur Qualitätssicherung her und ist um einiges grösser als Loepfe. Rund 680 Mitarbeitende beschäftigt Uster Technologies, etwa die Hälfte arbeitet im Zellweger-Areal in Uster, was das Unternehmen zum grössten privaten Arbeitgeber der Stadt macht. Bei Loepfe in Wetzikon sind rund 120 Mitarbeitende tätig. Über Umsatzzahlen schweigen sich sowohl Maccabruni als auch Kleindorp aus.
Aber sie machen kein Geheimnis daraus, dass die Zeiten herausfordernd sind. Das Textilgeschäft ist zyklisch. Markus Kleindorp: «95 Prozent aller Textilien sind Kleider. Der Absatz von Kleidern hängt von zwei Faktoren ab: Bevölkerungszahl und Wohlstand.» Geht es mit der Wirtschaft aufwärts, kaufen die Leute neue Kleider. Harzt die Konjunktur, wird zuerst bei der Kleidung gespart. Mit Folgen für die Hersteller von Textilmaschinen und Maschinenteilen. «Die Schwankungen bei den Auftragseingängen sind riesig und können 50 Prozent oder mehr betragen», bestätigt Davide Maccabruni.
Dazu kommt, dass die Produktionskapazitäten in der Textilindustrie in den letzten 20 Jahren verdoppelt wurden. Die Weltbevölkerung wuchs (glücklicherweise) nicht im selben Tempo. Als Konsequenz gibt es zu viele Textilmaschinen auf der Welt. Und da eine Textilmaschine eine Lebensdauer von rund 20 Jahren hat, verschwinden diese Überkapazitäten nicht über Nacht. Markus Kleindorp: «Die Durststrecke dauert jetzt zwei Jahre. Wir können nur warten, bis der Motor wieder anspringt.»
Doch diese Schwankungen gab es schon immer, die Textilindustrie ist es gewohnt, sie auszuhalten. Loepfe beispielsweise arbeite in der Produktion mit temporären Mitarbeitenden und einem erhöhten Automatisierungsgrad, erklärt Kleindorp. So bleibt man flexibel. Zudem können bestehende Anlagen auch mit neuen Messgeräten modernisiert werden, ein willkommenes Zusatzgeschäft in schwierigen Zeiten.
«Der Wettbewerb hält uns fit»
Dass sich gleich zwei Oberländer Unternehmen in dieser Nische der weltweiten Textilindustrie bewegten, habe sich «zu einem willkommenen Status quo entwickelt», sagt Maccabruni. «Der Wettbewerb hilft beiden Unternehmen, fit für die Zukunft zu bleiben.»
Die Situation ist vergleichbar – wenn auch in deutlich kleinerem Massstab – mit Basel, wo sich Pharmaunternehmen täglich messen, oder früher Detroit, wo die grossen US-Autobauer GM, Ford und Chrysler um Marktanteile und Talente kämpften.
Es gibt keine Zusammenarbeit zwischen Uster Technologies und Loepfe. Das heisst aber nicht, dass es keine gemeinsamen Interessen gibt. «Wichtig für uns beide ist, dass die Garnreinigungstechnologie im Spinnprozess relevant bleibt», sagt Davide Maccabruni.