How to master challenging fault occurrences like foreign matter accumulation
PRISMA's unique F-cluster feature
The PRISMA system is designed to increase machine efficiency, while maintaining yarn quality, even for challenging fault occurrences – like foreign matter accumulation.
Cluster events aren't limited to NSLT clearing. In fact, foreign matter faults can also occur in periodic or non-periodic cluster formations. While small foreign matter faults below the normal set clearing curve are seemingly harmless, their irregular accumulation can be disturbing in the final product and lead to costly customer complaints. This makes it all the more important to securely detect such events.
PRISMA’S unique F-cluster feature
With its innovative "F-Cluster" feature, PRISMA detects and eliminates repeating F faults that occur in clusters quickly and efficiently. Not only does the system cut out these disturbing faults as soon as they reach their maximum limit, within a defined set length, but it also ensures that highly contaminated bobbins are flagged for ejection with an alarm status. This guarantees the secure removal of offstandard bobbins from further processing.
Thanks to individually definable numbers of repeated F-Cluster events, precise and customized offstandard bobbin settings are achieved - reducing yarn waste while maintaining an optimal balance between quality and productivity. Plus ensuring faulty materials do not slow down the production line.
Benefits
- The accumulation of small foreign matter is detected and reliably removed, preventing costly claims.
- Immediate alarm status for strongly contaminated bobbins, such as offstandard bobbins.
- The system executes a cut only when the predefined maximum number of errors is reached, to ensure a minimum number of cuts and waste.
- Maximum flexibility due to individual cluster settings for observation length and number of faults.
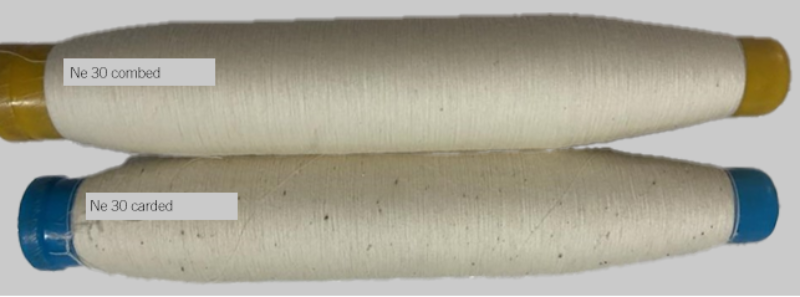
How do F-cluster faults occur?
- Colored foreign matter contamination: The majority of cotton contamination occurs prior to the pressing of the cotton bale. Colored foreign matter gets into the cotton which is torn into many individual parts by the spinning process.
- Organic matter contamination: Organic matter contamination mainly appears in natural fibers like cotton and consists of leaves, branches and seed coats that enter the spinning mill through the harvesting process and cannot be completely removed.
- A maintenance worker touches a bobbin with dirty hands, such fingerprints result in cluster pattern fault formations.
- Oil or grease contamination gets on the material through the rotating parts of the machines.
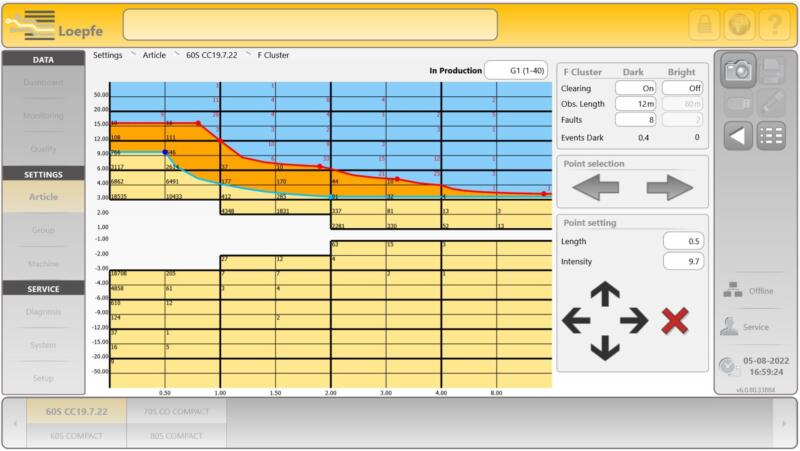
Setting Example
The following example illustrates the importance and function of this feature. The feature is especially valuable for spinning mills that produce the same count but differ in the process, i.e. carded or combed. For customers with a manual fed round magazine winder, a bobbin mix-up by the operator can happen very easily. F-Cluster is used in this case as it is the only way to distinguish different processes, usually due to the higher contamination with organics in carded yarns.
In a trial, a combed and a carded bobbin was used. The carded bobbin is contaminated with more seed coats, structural variation and a different fiber color compared to the combed yarn.
The settings were adjusted to the combed yarn. The combed yarn was replaced with a carded yarn to investigate and show the influence on the yarn clearer.
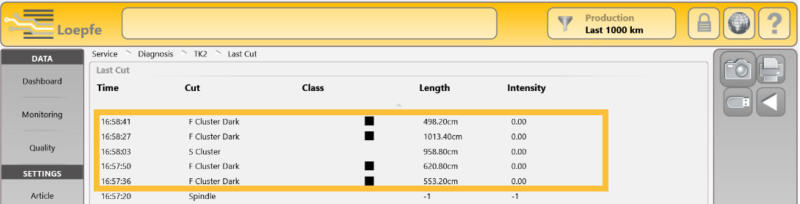
The carded bobbin was immediately detected and cut in the F-Cluster channel within 12m.
The organic faults and the structural variation of the carded bobbin are detected in the F-cluster dark area, demonstrating that such repetitive faults can be well detected in the F-cluster.
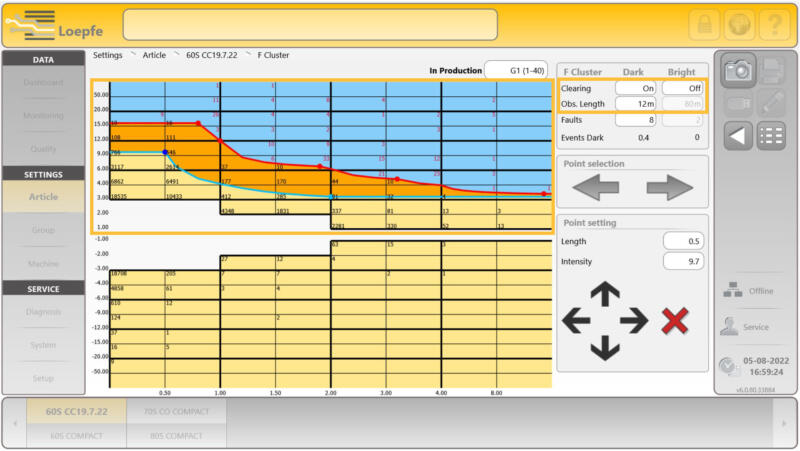
Find an appropriate setting
1. Switch cluster settings Dark or Bright “On“ (Article > F Cluster) and set the observation length and faults according to the below recommended marked setting.
2. Adjust the blue F-cluster curve according to the recommended marked setting below by touching the matrix.
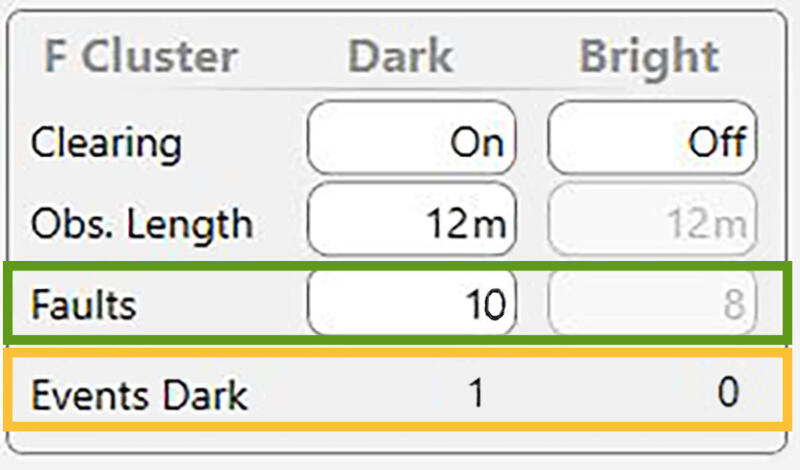
4. Use the number of “Events” as a guide to fine-tune the number of max. allowed “Faults” (marked below in green).
According to experience, the number of “Faults” should be set a minimum of 10 times higher than the “Events”, to avoid too many cuts. For example: if the number of “Events” is 1, the number of “Faults” should be set to 10.
5. Verify the cuts in Test mode for further fine-tuning of the setting.
Expert tip for fine-tuning the setting
Observation Length:
If the Obs. Length is set longer, the setting becomes more sensitive, and thus more cuts are triggered. The reason for this is that the probability increases that the defined number of faults will occur in this longer Obs. length.
Faults:
When the number of faults in the setting is lower, the setting becomes more sensitive, and thus more cuts are triggered.