How to eliminate strippiness and moiré effects
NSLT Cluster faults are events below the normal NSLT clearing limit which are not disturbing on their own. However their irregular accumulation or periodical appearance will cause complaints in the downstream process.
Such diameter and mass fluctuations are recognized as moiré and are easily visible on a blackboard (Figure 1) and in the final fabric.
The possible source for the faults is mainly coming from the ring frame, for example, defective top rollers (Figure 2), aprons, blocked compacting systems etc.
Periodic faults are disturbing in the final fabric and could lead to the fault patterns known as moiré and strippiness. Non-periodic small fault accumulations are also disturbing and can lead to an uneven fabric appearance. With the unique Cluster feature, available for neps, short, long, and thin clusters it is possible to detect reliable off standard bobbins with such kind faults.
Thanks to the simultaneous optical and mass sensor measurement, 100% of the yarn is always double-checked. This technique accurately detects the occurrences of periodic and non-periodic cluster faults.
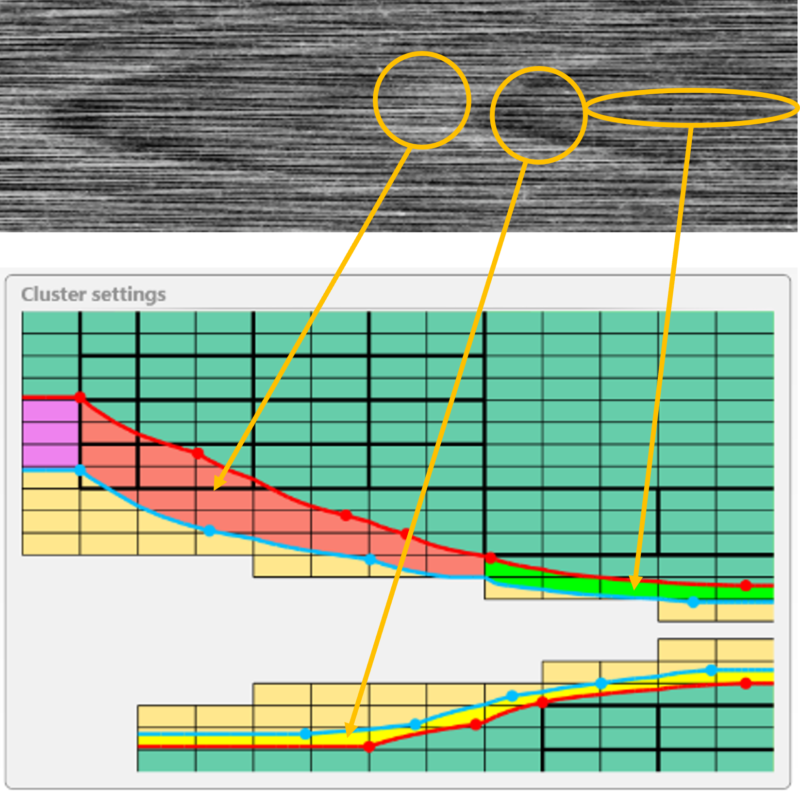
Periodical short, thin and long pattern which can be detected with the PRISMA Short/Long/Thin Cluster in the red/green/yellow area:
PRISMA serves the customer with the following benefits:
- Increased winding efficiency and yarn quality through the early intervention of the system
- Clearer cuts are initiated as soon as the predefined max number of faults is reached, which leads to a reduction in yarn waste
- Maximum flexibility due to individual cluster settings for neps, short, long, and thin places, each with its own observation length and number of faults
- Reduced quality waste in combination with the Off Standard Bobbins alarm

Setting Example
Irregular accumulations and periodical faults can be detected with NSLT Cluster. The clearing can be switched On or Off for individual cluster channels.
Observation length and No. of faults can be set accordingly.
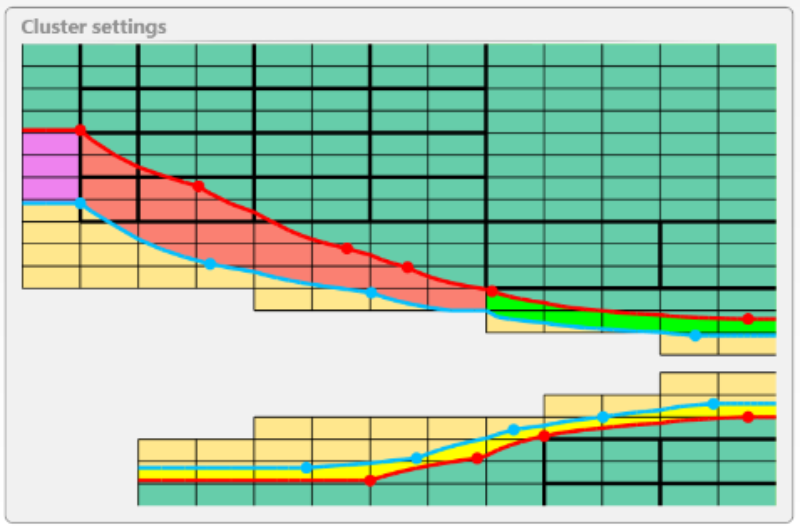
Explanations of the setting options
Clearing:
Switch the clearing on or off for each individual cluster.
Obs. Length:
The observation length for the max. allowed number of faults can be selected separately for the detection of each cluster area.
Faults:
The number of faults can be set separately for the detection of each cluster area. (see below for setting help)
Events:
The actual number of events are shown for each cluster area in the matrix. This value shall support the user in finding the optimal "Faults" setting.
The blue cluster clearing curve needs to be defined on the matrix, the more sensitive the cluster curve, the more faults will be cut.
- Purple – Nep Cluster area
- Red – Short Cluster area
- Green – Long Cluster area
- Yellow – Thin Cluster area
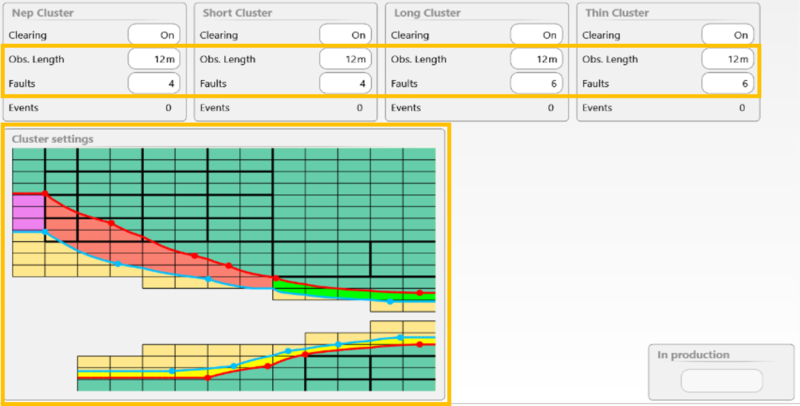
Find an appropriate setting
1. Switch cluster settings “On“ (Article > NSLT Cluster) and set the observation length and faults according to below recommended marked setting.
2. Adjust the curve according to the recommended marked setting below by touching the matrix.

3. Wind 100km to get a sufficient number of shown "Events”
4. Use the number of “Events” as a guide to fine tune the number of max. allowed “Faults”
According to experience, the number of the “Faults” should be set a minimum of 10 times higher than the “Events”, to avoid too many cuts. For example: if the number of “Events” is 1, the number of “Faults” should be set to 10.
5. Verify the cuts in Testmode for further fine tuning of the setting.
Expert tip to fine tune the setting
Observation Length:
If the Obs. Length is set longer, the setting becomes more sensitive and thus more cuts are triggered. The reason for this is that the probability increases that the defined number of faults will occur in this longer Obs. length.
Faults:
When the number of faults in the setting is lower, the setting becomes more sensitive and thus more cuts are triggered.