How to successfully produce a core yarn
PRISMA’s core yarn feature
Producing a core yarn successfully involves many challenges. Core yarns consist of a minimum of two components, the core as filament within the center of the yarn, and the sheath material. In addition to the normal yarn defects, missing and offcenter cores need to be correctly recognized. Providing a yarn with a missing or an offcenter core often causes problems within the downstream process and leads to costly complaints.
PRISMA is the solution, combining its unique simultaneous dual measurement with its core yarn features. Thanks to the simultaneous optical and mass sensor measurement, 100% of the yarn is analyzed in regard of mass and hairiness variations. This technique accurately detects the occurrences of missing and offcenter cores.
An offcenter core and a missing core have an influence on the hairiness respectively on the mass. The following images show the principle of detection:
In addition to the unique measurement methodology, PRISMA also provides setting support. Thus, PRISMA creates a suitable core yarn setting proposal based on the settings of the yarn parameters and core properties. Providing the operator with maximum support for successful core yarn production.
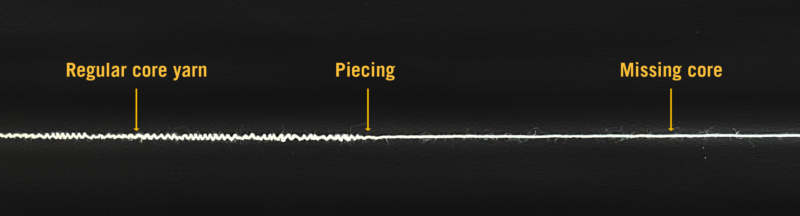
PRISMA provides core yarn producers with the following benefits
- Most accurate detection of core defects
- Reduction of costs and complaints through efficient detection of core defects
- Increased raw material utilization, reaching the best quality with the existing material
- Ease of use through the setting proposal and the specific core yarn matrix
- Great flexibility for spinners who frequently switch between conventional and core yarns as the core yarn detection is an individual feature
- The Missing Core and the OffCenter Core feature are standard equipment of the PRISMA DM sensor type
- Both features work for all types of core yarns
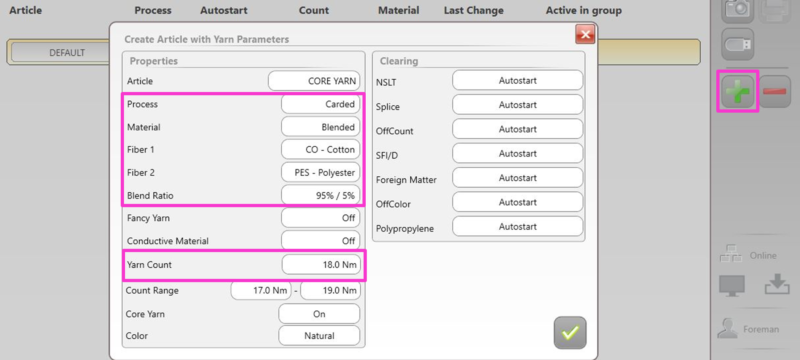
Setting Example
Enter all the correct article properties for the core yarn.
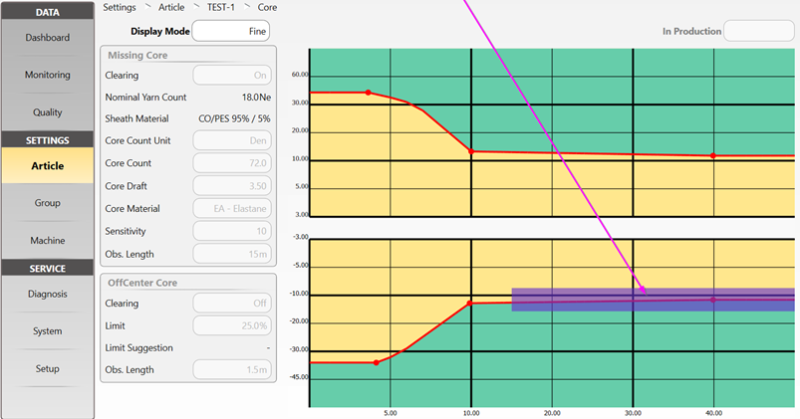
Enter all the correct core properties. The intelligent system calculates the expected range for the missing core faults in the count matrix, the purple field in the matrix indicates the range.
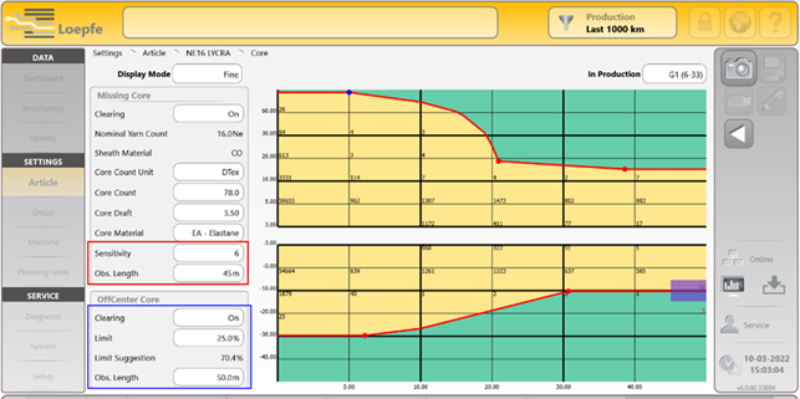
Missing Core:
Set the minimal observation length and optimize the sensitivity until the missing core gets detected. To raise the sensitivity level increase the number within the sensitivity field. “see highlighted in red”
OffCenter Core:
Set the observation length and optimize the limit until it gets detected. To increase the sensitivity, reduce the % number within the limit field. “see highlighted in blue”
First verification of the setting with faulty sample bobbins:
- Produce bobbins without core or with offcenter core, use these bobbins only to compare with bobbins of the same ring frame doff running on the winder
- Try the faulty sample bobbins at different single winding positions to check if the fault is detected. Always use the automatic bobbin change to feed the faulty bobbins.
- Adjust and finetune your settings until the faulty bobbin is always detected and the good bobbin is running.
- For the next ring frame doff you must produce and use a new faulty bobbin sample to use this as a new reference for the current ring frame doff.
Reason: Good and faulty bobbins should only be compared within the same doff, because on the one hand the quality of the material can vary. On the other hand, the faulty bobbin should not be used more than once, because it could be stored in a different place and a different climate could influence the material, and thus the bobbin would no longer be comparable.
Second verification of the setting with Testmode:
Use the Testmode to verify missing and off centric core cuts in the normal winding process.