Maximize machine efficiency through proper cleaning implementation
MillMaster® TOP Lab Trend preventive maintenance
Cleaning presents a complex and costly challenge in the context of a spinning mill, particularly when dealing with short staple fiber yarns that tend to generate a significant amount of fly. Neglecting timely cleaning efforts can subsequently lead to an increase in disturbing yarn defects, which adversely affect yarn quality, machine efficiency and ultimately profitability.
Here the Lab Trend offers a concrete solution by identifying potential problems that arise from the machines in the production chain of a spinning mill. By comparing the error distribution with the table “Classification of yarn defects and their sources”, the cleaning intervals can be adjusted promptly. This proactive approach not only improves yarn quality but also optimizes machine efficiency, increasing overall profitability.
Proper cleaning implementation
In the example illustrated, it becomes evident that winding machine 201 exhibits a consistent and concerning upward trend in the occurrence of disturbing yarn faults within class B2. The winder 201 sees a significant increase, with the number of B2 faults reaching a high of 461. In contrast, the remaining machines maintain a relatively low count of fewer than 100 B2 faults over the same time frame.
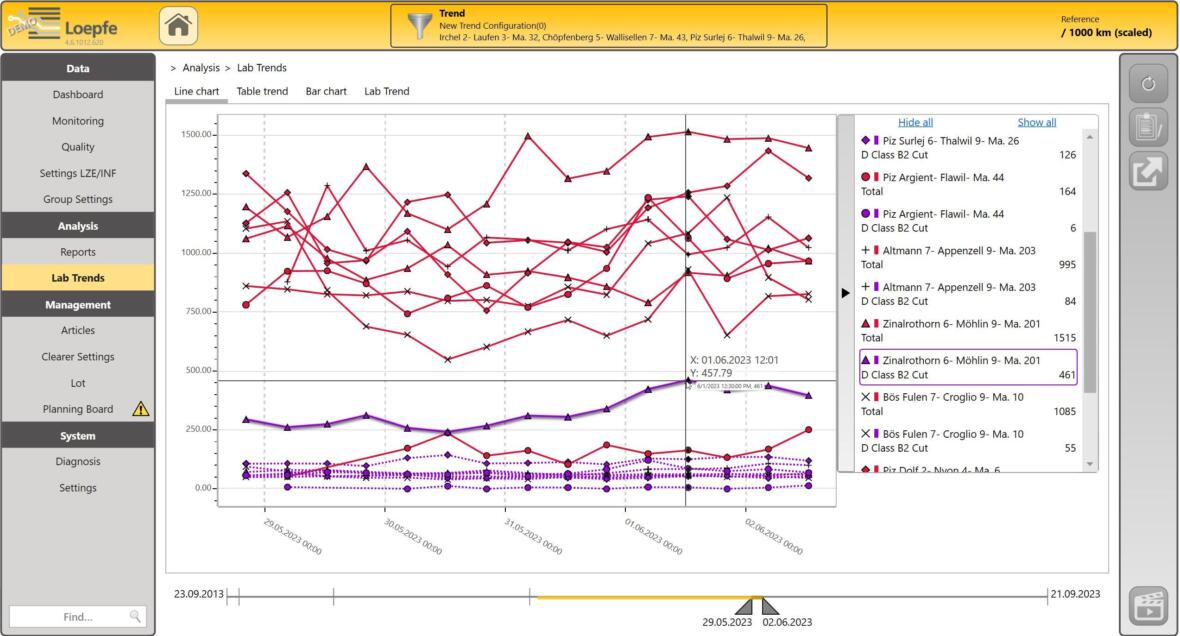
It's time to address this issue by referring to the Loepfe "Classification of yarn faults and their sources" chart.
A rise in yarn faults classified as B2 typically indicates that the cleaning intervals at the ring spinning machine which is connected to the winding machine 201, have been too infrequent. To prevent a further escalation of yarn faults and, consequently, a significant drop in winding machine efficiency leading to increased downtime, it is strongly recommended to increase the cleaning cycle of the linked ring spinning machine and the winding machine number 201.
Reasons for rising faults in the class B2:
- Unclean drafting unit at ring spinning frame
- Fiber fly accumulation due to improper maintenance in the ring spinning department